Just in Case Definition Business
Just-in-time (JIT) and just-in-case (JIC) are on opposite ends of the inventory philosophy spectrum: One aims for lean operations, the other makes stockpiling a priority. Both are commonly employed in manufacturing and distribution, but any business providing tangible products, such as retail or food and beverage, falls somewhere on the JIT versus JIC curve.
No matter the industry, making the most of inventory requires planning and a solid grasp of current and future customer demand. There are several points about JIT and JIC inventory management that companies should understand to successfully carry out either just-in-case or just-in-time inventory learning objectives or a combination of both.
Choosing Between Two Inventory Management Strategies
Companies committed to just-in-time inventory focus on making the supply chain as lean as possible. It's a reactive strategy, where inventory purchasing decisions are based on current conditions.
In contrast, those that prefer a just-in-case inventory approach are proactive. Purchases are made to maintain a healthy stockpile and avoid running out of raw materials or work in progress items and slowing or stopping production.
A JIT model is something to aspire to because it aims for a sustainable process, with reliable suppliers and stable demand. JIC is suitable for cases where having adequate inventory is nonnegotiable. JIC companies are often more agile and able to respond to sudden demand increases.
For both JIT and JIC, the term "inventory" refers to raw materials and supplies used in production, unfinished items in various stages of the manufacturing process and final products.
Examples of unfinished, or work in progress, items include motherboards with CPUs installed that are ready to have memory modules attached in the next stage of building a laptop.
What is just-in-time (JIT)?
In inventory management, "just-in-time" means having inventory arrive precisely when needed, no sooner. Another way of referring to JIT inventory management is as a "pull" system. A pull system means supplies are replaced as goods are consumed rather than proactively.
Just-in-time inventory management consists of two core principles:
- Materials must arrive when production is expected to begin.
- Materials should not arrive before production is expected to begin.
These are important distinctions because production can't go forward without inventory, but the business can incur storage costs if the inventory arrives too soon.
The goal of a JIT inventory strategy is to balance production volume with inventory levels and ensure the company keeps only the stock that's necessary for near-term work on hand. It's an effective method for attaining high production levels with minimal inventory holding and supply costs.
This inventory strategy works best when a company works with reliable suppliers that provide consistent quality, doesn't experience shipping disruptions and pens long-term contracts that minimize price fluctuations.
One of the most significant downsides to just-in-time systems is that unexpected supply chain interruptions in any area can derail the entire process. For example, a sudden shortage of raw materials or bad weather that slows shipments may have a dramatic effect on production.
What is just-in-sequence (JIS) vs. just-in-time (JIT)?
Just-in-sequence (JIS) inventory management is a variation on JIT. The main differentiator between just-in-time and just-in-sequence (JIS) is that JIS ensures inventory arrives in the specific order in which it is used in production. JIS is associated with assembly lines, such as automotive or large appliance manufacturing, where items arrive at the line position at the time they're needed.
What is just-in-case (JIC)?
Just-in-case inventory strategies are based on expected sales and require companies to purchase supplies proactively to meet any level of demand, within defined parameters. Businesses that use JIC may avoid the effects of common inventory management challenges such as supplier delays, unexpected increases in demand or spikes in the cost of a material or component.
Just-in-case inventory prioritizes preparedness over the cost and cash flow implications of holding stock in reserve. It protects businesses from falling behind in production or losing revenue because they couldn't meet demand.
This inventory management strategy pays off when demand is difficult to predict or a raw material or component is subject to sudden surges in price or going out of stock. It's also helpful in environments where suppliers aren't reliable.
A significant weakness of the JIC method lies in the fact that these systems can be wasteful if demand slows down and inventory stagnates. You're also tying up cash.
Just-in-Time vs. Just-in-Case: Pull vs. Push
Companies use just-in-time inventory to reduce excess supply and create a lean production process, while just-in-case inventory is used to avoid running out of stock due to a sudden increase in demand. Both strategies provide companies with benefits, but there are drawbacks, as well.
Just-in-time
Just-in-time inventory management optimizes the supply chain, but there are caveats.
Advantages
Just-in-time inventory benefits those with efficient operations and is good for the bottom line. This strategy also prevents overproduction and minimizes transport costs. Other benefits:
Efficient use of resources: JIT inventory management reduces the risk of overordering and having supplies sit idle. This allows the company to divert resources from that inventory to other business areas.
Less waste: There is less waste as businesses keep only the stock they need for production. That is particularly helpful for businesses depending on perishable supplies.
Reduced costs: Eliminating overbuying reduces supply costs directly since companies only purchase what they use immediately. Eradicating stagnant inventory also cuts warehousing expenses, including labor and administration.
Increased agility: Using JIT reduces the amount of time it takes to change over inventory when fluctuations in demand occur or products change.
Disadvantages
Just-in-time inventory management can increase issues in some key areas. For example, when using JIT, companies order bare minimums of items based on projections. However, if there's a sudden, unexpected surge in demand, there may not be enough products or supplies on-hand. Other downsides:
Supplier stability needed: The success of a just-in-time inventory strategy relies on the timeliness and consistency of suppliers. However, companies have little control over supplier operations, and even previously reliable partners can experience disruptions that ultimately cause delays for the receiving company. Then there are unforeseen shipping delays to consider.
Inability to meet unexpected demand: The just-in-time inventory method also requires few to no fluctuations in demand. Some variations are predictable and planned for, such as seasonal trends, but unexpected spikes or valleys make it difficult to maintain the necessary stock stability.
Pricing risks: A JIT strategy can be more expensive than JIC if materials cost less during certain parts of the year, meaning stocking up would be prudent. Businesses may also lose out on savings because they don't take advantage of bulk-buying discounts.
Just-in-case
Companies that employ a just-in-case inventory strategy enjoy several benefits, but it is not without downsides.
Advantages
Just-in-case inventory management can facilitate growth and profitability in a few ways.
Increased competitiveness: Companies can keep up with most any level of demand, increasing their competitive edge and even boosting market share if they can meet demand when a competitor is out of stock.
Fewer lost sales: With JIC, companies reduce the risk of lost sales due to a lack of inventory. JIC inventory allows companies to continue production while waiting for stock to be replenished.
More wiggle room in demand forecasting: There is less need for precise demand projections because inventory levels are high enough to keep up with demand.
Savings: Companies can take advantage of bulk discounts or make large purchases when prices are lowest, decreasing direct procurement costs.
Disadvantages
Just-in-case doesn't address all inventory issues and creates a few of its own.
Additional storage costs: Companies incur more carrying costs to maintain the excess inventory. These costs can be high, equaling 20% to 30% of total inventory value.
Increased opportunity costs: Capital is tied up in inventory. That takes flexibility away from other aspects of the business and increases opportunity costs.
Wasted stock: There is an increased risk of stock spoiling or becoming obsolete if items don't sell. This risk is particularly significant if the goods are perishable, seasonal or part of a flash-in-the-pan trend.
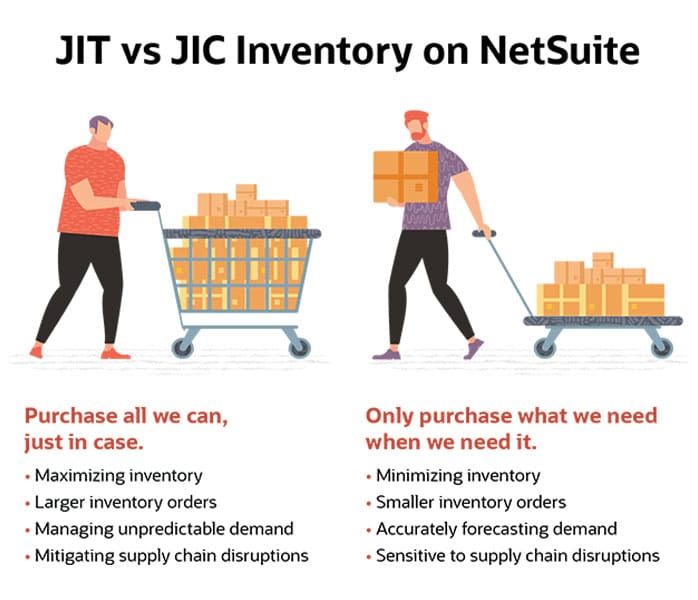
Just-in-Time vs. Just-in-Case: What's the Difference?
Just-in-Case | Just-in-Time |
---|---|
A "push" system where inventory purchases are not based on actual current demand. | A "pull" system where inventory is essentially purchased to order. |
Focuses on maximizing flexibility with less concern for capital application. | Focuses on minimizing inventory and using capital efficiently. |
Excess inventory is kept on hand to avoid running out due to supplier delays or demand spikes. | Inventory is purchased only to meet immediate production or sales needs. |
Companies generally make larger, more expensive inventory orders | Less working capital is required because inventory purchases occur in smaller batches. |
Valuable when demand is unpredictable or suppliers are unreliable. | Works best when demand is stable and suppliers are highly dependable. |
Demand forecasting is less critical as long as there is enough inventory to meet the highest demand. | Requires accurate demand forecasts to avoid over- or under-buying inventory. |
Choosing the Right Strategy for the Right Time: A Hybrid Model
There are more cons than pros from hewing strictly to either a JIC or JIT inventory management strategy. In the real world, they work best in tandem. Companies that develop a hybrid inventory management model that combines the buffer of just-in-case inventory with just-in-time's conservative use of capital can have the best of both worlds.
Employing a hybrid system
A standard method of employing a hybrid push-pull inventory system is to have some stages of the supply chain operate as pull systems while others operate in a push model. This strategy requires a more accurate demand forecast than a JIC system but doesn't aim to keep standing inventory at zero, as in JIT systems.
The main objective is to address long- and short-term production and sales needs by keeping inventory levels low enough to be cost-effective but high enough to withstand supplier or production delays or meet increased demand.
The first step is an inventory analysis exercise, where you classify items as, for example, vital, essential or desirable and then consider how scarce an item is and how easily you can acquire it, as well as the likelihood of spoilage or obsolescence.
Companies can employ JIC inventory for vital, quick-turnover items, ensuring stock is always available but constantly consumed. JIC can also be helpful for scarce items that are available only from unreliable suppliers or that are often out of stock or have long lead times.
Of course, you might also look to find a more reliable or backup supplier.
Companies use JIT inventory for less popular items or those that sell in small batches. For example, the customization stage of a personalized t-shirt order would benefit from a JIT approach since there is no need to keep a stockpile of made-to-order items. However, a JIC approach should manage the inventory of plain t-shirts awaiting printed designs.
Economic order quantity
Knowing how much inventory to purchase is essential to apply a push-pull inventory system effectively. The economic order quantity (EOQ) formula helps this hybrid method of inventory management determine the optimum amount of stock to purchase.
It's written as:
EOQ = √KM/H
"K" represents the costs of inventory orders, "M" represents the amount of inventory used in a given period and "H" represents total inventory expenses — including warehousing, depreciation and opportunity costs — within the same period.
The resulting figure is the amount of inventory that a company should order.
Manage Your Strategy With Inventory Management Software
Successful companies integrate just-in-time and just-in-case inventory methods to achieve efficient, agile supply chain operations. This strategy creates a buffer allowing for an adequate response to unexpected demand or supplier issues while maintaining a minimal amount of inventory and keeping costs low.
However, ensuring that demand forecasts are accurate and optimizing the supply chain to ensure reliable operations is critical to either approach.
Modern enterprise resource management (ERP) software supports both JIT and JIC inventory to account for both push and pull. It provides granular and birds-eye views of current inventory levels, inventory in the pipeline and future demand. Look for a system can also gather and analyze supplier, inventory turnover and demand data to generate more reliable forecasts.
Agility, cost savings and the ability to meet demand are three pillars of effective inventory management. Getting the balance between JIT and JIC right can overcome many challenges, from shifting customer demand to limited visibility to poor production planning.
Just in Case Definition Business
Source: https://www.netsuite.com/portal/resource/articles/inventory-management/just-in-time-vs-just-in-case.shtml
Belum ada Komentar untuk "Just in Case Definition Business"
Posting Komentar